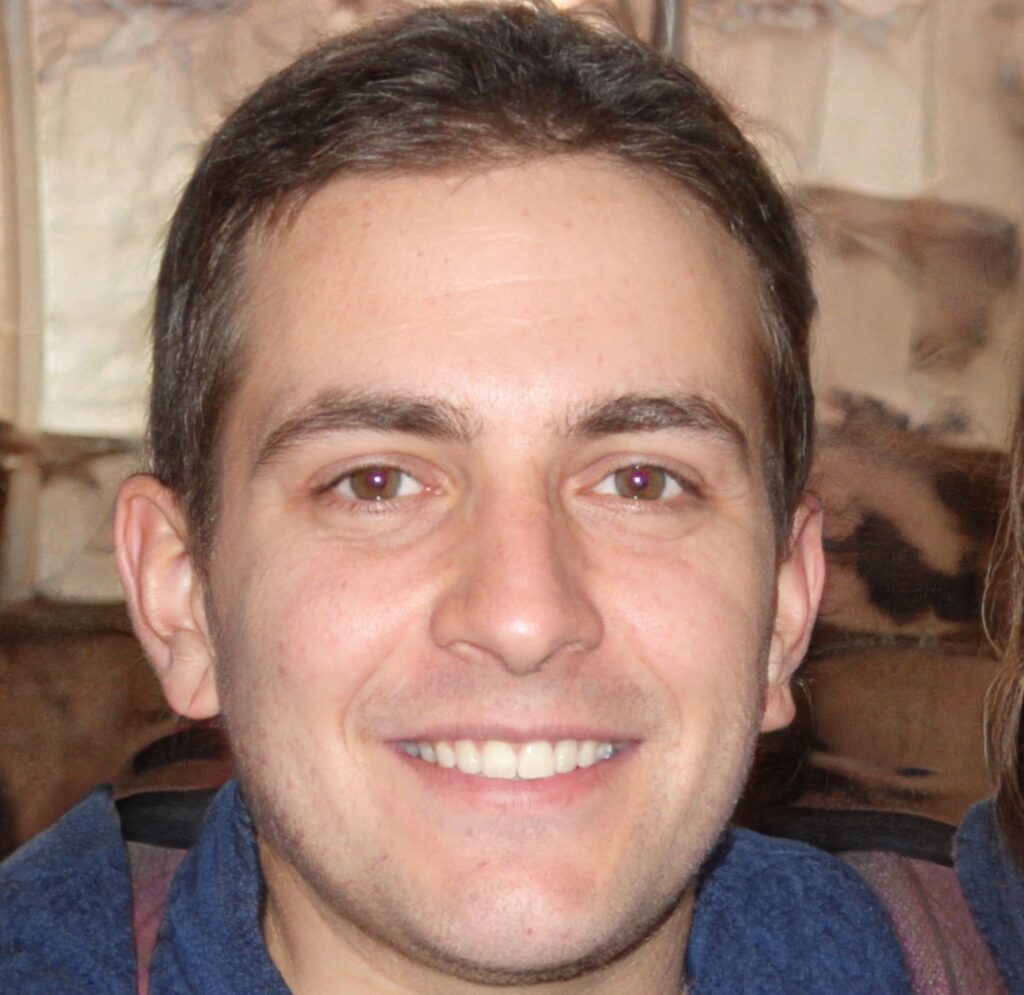
Bem-vindo ao SyncGameTech, o seu destino ideal para explorar o fascinante universo dos jogos e as mais recentes novidades na plataforma Roblox!
Fundado por Lucas Mendes, conhecido como SyncGameTech, este influente YouTuber de jogos estabeleceu o blog após mudar-se para o Portugal. Originalmente um ávido jogador de Fortnite, Lucas encontrou no Roblox uma nova paixão para compartilhar seu conhecimento e entusiasmo pelas infinitas possibilidades dentro deste mundo de jogos.
No nosso blog, SyncGameTech, você encontrará análises detalhadas dos jogos mais quentes do momento, notícias sobre atualizações recentes e tudo o que há de novo no Roblox. Nosso objetivo é fornecer informações precisas e valiosas para enriquecer sua jornada pelo universo Roblox.
A SyncGameTech está aqui para auxiliar todos os jogadores, dos veteranos aos novatos, a explorar o vasto e diversificado reino dos jogos! Junte-se a nós nesta aventura emocionante enquanto exploramos novos mundos, testamos nossas habilidades e desfrutamos das melhores experiências que o Roblox tem a oferecer.